In these tough economic times money is tighter than ever and getting a roof right first time has never been more important. If a contractor must go back to rectify problems, most, if not all the profit made on a job may be lost; in some cases, it may result in the contractor not being paid at all. So, getting it right first time is crucial.
Design
The successful installation of a good roof starts with design. A roof should be designed with the type of roof covering in mind, for example slates, plain tiles, interlocking tiles, etc. But, beware of the risks that product substitution can bring. Taking the example of double lapped plain tiles; with such a versatile material, the designer can incorporate features such as curves, eyebrows, small vertical sections, etc. Problems would arise though, for example, if a single lap tile is substituted when the building design includes a curved roof section. Then, the roof must be ‘faceted’ to create a series of flat planes; meaning a series of very shallow hip or valley details, which are very difficult to detail properly.
Beware of designing roof faces with over-long rafter lengths, particularly when using flat single lap tiles at low pitches. Tile manufacturers give maximum recommended rafter lengths for their products, with guidance on increasing the roof pitch for long rafter lengths.
Avoid designs where water is discharged from a higher roof slope onto small lower roof areas, or into another junction such as a side abutment. If practical, design the building to break up the roof into smaller sections. For example, allow the upper roof to shed directly into a gutter, rather than onto a lower roof.
Sometimes the pitch on adjacent roof slopes roofs can vary. This will mean that tile courses do not line up at hip and valley junctions without forward planning; it would be necessary to set out the battens on the lesser pitch first and then line up the battens with these on the steeper pitch.
Features such as raking verges can look architecturally interesting but remember that if the rake is such that water will run off it, then it is really a sloping eaves and will require a gutter system. If the rake is the other way, then it is really a sloping mono-pitch roof, and so needs a top edge weathering system.
Installation
A good roof installation starts with the underlay. Underlay must act as a second line of defence against wind driven snow, rain or dust, as well as making the building weathertight before the tiles are installed. It is also worth considering the use of nail tape and counterbattens. Nail tape seals between the underlay and battens and counterbattens encourage air flow within the batten cavity and provide a gap for any water to flow under the tile battens.
It is important to ensure the underlay is weathertight at junctions such as side abutments, valleys and around roof windows and chimneys and is properly supported at the eaves, with adequate fall, behind the fascia or tilt fillet. If water pools behind the fascia it will find its way through any cuts or holes and eventually rot the underlay, causing leaks.
The fascia height should be set to allow the eaves course tiles to lie at the same pitch as the general tiling. Avoid sprocketed, or bellcast eaves with single lap tiles. With plain tiles, the general roof pitch must be steep enough to allow the sprocket to be at or above the minimum recommended roof pitch for the tiles.
At side abutments, fit the flashing appropriate to the tile or slate. For example, slates and plain tiles require soakers, cover flashings are generally used with single lapped profiled tiles and secret gutters with flat single lapped tiles.
Construct valleys to cope with the volume of water likely to be shed from each roof face, with the appropriate valley width, upstands and side welts etc. Do not rely on mortar bedding to prevent water ingress in open valleys.
On roofs with flat tiles, rainwater is prone to run over the verge edge therefore, when using a bedded or cloaked verge tile finish, the construction must be set far enough over the gable to prevent water running down the gable wall. If using a dry verge system, check that it complies with BS 8612, which means that it is designed to prevent water from running down the wall.
The use of dry fix systems will minimise future maintenance of hip and ridge lines. But where mortar bedding is required, the ridges and hips must also be mechanically fixed using nails, screws or clips to prevent to risk of dislodgement if the mortar bed subsequently fails.
Like most manufactured products and indeed, natural products, there is inevitably a degree of colour and texture variation between batches. Therefore, it is important to mix tiles from several pallets on the roof to achieve a satisfactory finish.
Lastly, it is important to secure the tiles using the appropriate fixings. The tile manufacturer will provide fixing recommendations that will ensure a long lasting and secure roof covering.
Summary
- The roof tile manufacturer can supply a complete roof specification. Always obtain a mechanical fixing schedule to minimise risk of future wind damage.
- If specifying non-standard details or products, work closely with the manufacturer to develop suitable detailing.
- Design the detailing correctly and get it right during construction. Make sure the contractor is experienced in the work being undertaken.
- Remember that the price for rectifying a faulty roof can far outweigh the cost of installing it right in the first place.
John Mercer: January 2023
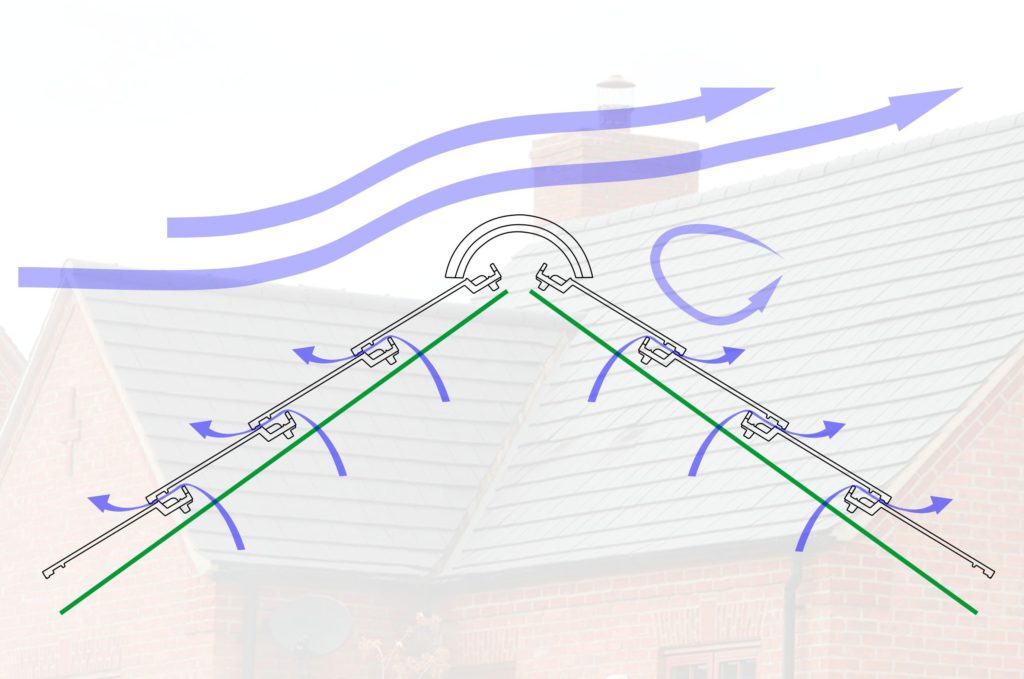