All roof coverings and underlays need to be replaced at some point during a building’s useful life. When that time comes, how can the next generation of roof membranes help existing buildings to meet current performance requirements and be resilient for the future? Pamela Howat, Senior Technical Advisor at A. Proctor Group looks at some of the challenges of retrofitting roofs.
Perhaps the biggest challenge presented by existing buildings is that no two projects are ever the same. The construction method and the quality of the construction, combined with site specific factors that affect exposure to weather, all influence the durability of a roof. Any resulting water ingress will have a further negative impact on
lifespan.
Then there are occupancy factors to consider. How people use a building – the way they heat and ventilate it – varies from occupant to occupant. That changes how the building fabric responds to different internal conditions, shortening or prolonging a roof’s service life accordingly.
Retrofitting a roof isn’t just about the roof
Retrofit is all about managing risk. One of the most important things to keep in mind when retrofitting an existing building is that everything is interconnected. This is reinforced in all retrofit guidance, as well as standards like BS 5250:2021 Management of moisture in buildings – Code of practice.
It might be tempting to look at the roof in isolation, but decisions enacted elsewhere will impact on the behaviour of the roof. Making other parts of the building fabric better insulated and more airtight will improve the building’s energy efficiency. But if corresponding improvements to ventilation provision are not made then a build-up of moisture vapour internally could transfer into the roof space. And improvements carried out to the roof will affect the design and specification of future changes to other parts of the building. Loft insulation is seen as ‘low hanging fruit’ when it comes to retrofit. Often it is the first place that people start when improving the performance of a building, but it carries its own risks for the roof as a whole.
What to consider when making improvements to pitched roofs
Installing loft insulation, or increasing the thickness of any existing loft insulation, is a relatively easy measure to carry out. Homeowners might even
consider doing the job themselves to keep costs down. Questions that need to be considered when upgrading loft insulation include the following.
- What is the type, age and condition of the existing roof underlay?
Is the roof underlay a traditional high-resistance (HR) membrane, like bitumen felt? If so, is it due (or even overdue) for replacement?
Is it a more modern low-resistance (LR) membrane? If so, it is likely to be relatively new and a complete replacement of the roof covering probably isn’t needed yet. But it is also likely to be an airtight LR membrane, so whilst it allows vapour diffusion through the membrane it doesn’t have the additional benefit of air passing through the underlay which enhances’ moisture removal.
Making loft insulation thicker has the effect of reducing the temperature of the roof space, because heat loss into the roof is reduced. Typical loft insulation products are vapour permeable, so internal moisture can still reach the roof space. Colder air holds less moisture, making condensation more likely within the roof space – even if the underlay is a (LR, airtight) ‘breather membrane’. - How is the roof space ventilated?
Once internal moisture vapour reaches the roof space, it is critical to remove it from the building as quickly as possible. This is where effective roof ventilation comes in, dealing with the increased humidity that comes from making the roof space colder.
Roof space ventilation might be at the eaves only, relying on air movement across the span of the loft. Or it might be at the eaves and ridge, with air flowing up through the roof space. Assessing the existing provision prior to carrying out work is an essential part of responsible roof retrofit.
A significant issue with upgrading loft insulation is whether it can be installed without blocking existing eaves ventilation. The counter-issue to keeping ventilation pathways clear is making sure that gaps around the perimeter of the roof don’t act as a route for warm air to escape from occupied rooms below.
Proctor Air®: an air permeable LR membrane ideal for retrofit projects Because every retrofit project is different, performance targets and available budgets are different, dictating the scope of work that can be carried out. Nevertheless, the overarching aim of many retrofits, and especially deep retrofits, is to prepare existing buildings for the future.
That’s where A. Proctor Group’s new pitched roof underlay comes in: Proctor Air.
As an air permeable (rather than airtight) LR underlay, no VCL is required in the ceiling. And no ventilation measures are required in the cold roof space, so insulation can be installed right into the eaves with no risk of blocking ventilation.
Proctor Air permits the passage of both air and moisture vapour through the roof construction, providing a more uniform flow of air than normal vents. Condensation risk in the roof space is therefore removed.
When a new roofing system is installed, there is an inevitable period of time where the underlay is in place without the roof covering to protect it. The underlay bears the brunt of any inclement weather, and its ability to do that is particularly critical in retrofit scenarios where the building is likely to still be in use.
Proctor Air’s water resistance has been tested and meets the threshold of over 1m of water holdout recommended in the NFRC’s Technical Bulletin TB06. During installation, where periods of severe inclement weather, or prolonged exposure, is expected BS5534 and BBA Bulletin 2 advises that temporary protection is considered. This is especially important to consider in a retrofit situation where the occupants are likely to remain in residence or there are sensitive internal finishes etc.
A. Proctor Group is a 4th generation family business with a history of technical innovation, promoting good practice, and developing products that roofing contractors want to use. We have applied this wealth of experience to creating the next generation of air permeable LR membrane.
All of this is backed by our unique 15-year warranty, offering peace of mind even in the face of an uncertain future climate. For more information visit:
https://proctorgroup.com/products/proctor-air
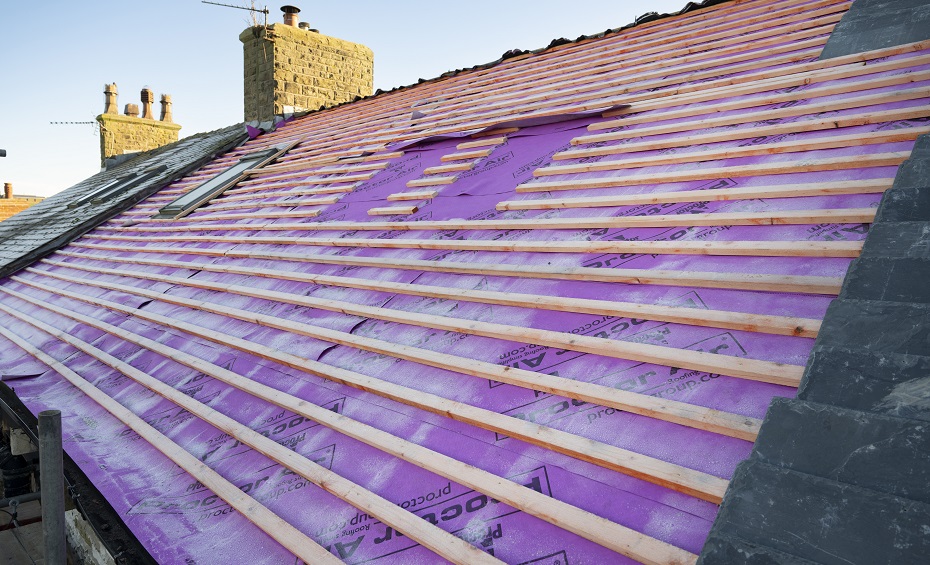
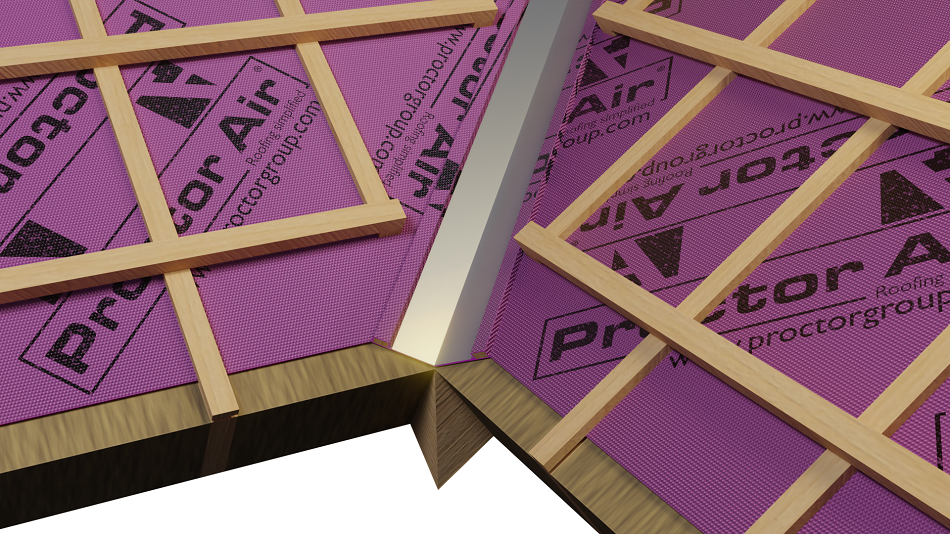