By Jacob Hill, Technical Manager, Wienerberger
When I tell people I work in design for a manufacturer of roof tiles, I always receive the same response, “Isn’t a roof tile just a roof tile?”. However, the reality is a lot of work goes into the design of every roof tile Wienerberger produce. From experience in other industries, I can confirm as much thought goes into the design of a roof tile as any other product, from automotive through to kitchen appliances. The process, techniques and skills applied are all transferable.
All of Wienerberger’s products go through an extensive design process prior to release. For those interested in design, how things work, or simply want a little more insight into the products you use, I write this to provide a little appreciation into some of the work that accompanies the design of a roof tile. A component which to many, hasn’t changed for decades.
One of the most common misconceptions is why manufacturers change the design of their tiles. The most common reason is the renewal of key components that are used in production. Concrete tiles are commonly made on pallets, pieces of metal on which the concrete is placed, forming the underside of the tile. Clay tiles are typically made using top and bottom moulds, into which the clay is pressed or extruded. Whether pallets, moulds or other, these components wear over time and require replacing. The number of these components required to manufacture the quantity of tiles Wienerberger produce requires a significant investment. Therefore, before that investment is made, we take the opportunity, where possible, to improve the design. Improvements may include making the tile lighter but stronger, easier to install, lay at a lower pitch, whilst also attempting to incorporate any improvements that installers may have suggested over the life of the previous design.
Traditionally the design process begins in the heart of the factory, using years of expertise to input into the next design iteration. More recently, this expertise has been supported in the virtual environment, using computer aided design to draw what the new tile will look like in 3D. Using these computer models, we are able to run computer simulations to calculate aspects like the strength of a tile, or the wind driven rain performance before a physical product has even been made. This process can rule out poor designs before any production time, or more importantly material, is wasted.
Taking the best designs forward, we look to make a physical tile, a prototype. This can take many forms, in some instances we still use traditional wooden handcrafted methods. However, the advancement of rapid prototyping, known to many as 3D printing, allows us to achieve more than ever before. We can physically see, touch and install a new design before any time or cost is spent in production. We can share these samples with customers and receive feedback, at which point we can modify the design if required before progressing to the next step, feasibility in production. This is where we turn the design into a finished product in the desired material, initially in small batches. Tiles from which we will use to conduct various tests such as the strength tests and wind driven rain test, allowing us to confirm the design works in practice. Once everyone is happy with each aspect of the new design, work begins to manufacture the tile in full production and make its way out to our customers.
The prototyping technology available to us is advancing rapidly, the cost to print plastic components is already on an affordable level for hobbyists and enthusiasts. Printing in metal is fast becoming more affordable, and even the first full size houses have been 3D printed, utilising a larger scale printer that prints in concrete! I have no doubt that in the near future we could see this technology print detailed roof tiles out of concrete and other materials. Soon gone could be the days of not being able to replace tiles no longer in manufacture. Need three replacement tiles? how about printing them?
For anyone interested in how roof tiles are made, Wienerberger’s factories are the place to visit, where you can see the process from raw material thorough to finished product. Prior to the pandemic Wienerberger encouraged our customers to come on a factory tour to see the manufacture of both clay and concrete tiles. Unfortunately, with existing restrictions we cannot currently offer this. However, if you are interested in such a tour, I would encourage you to contact your local area sales manager and we can hopefully welcome you once restrictions ease.
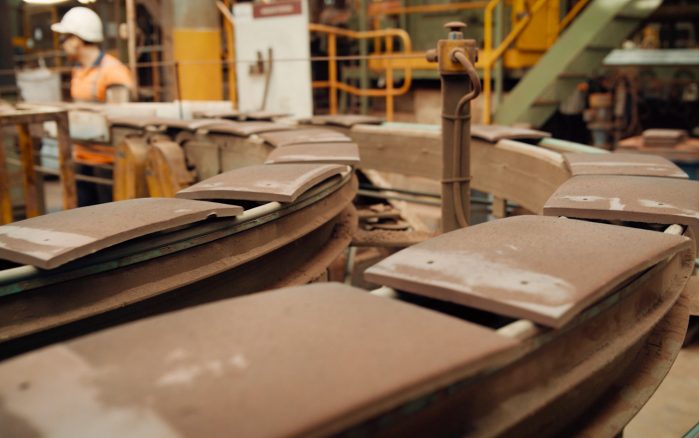
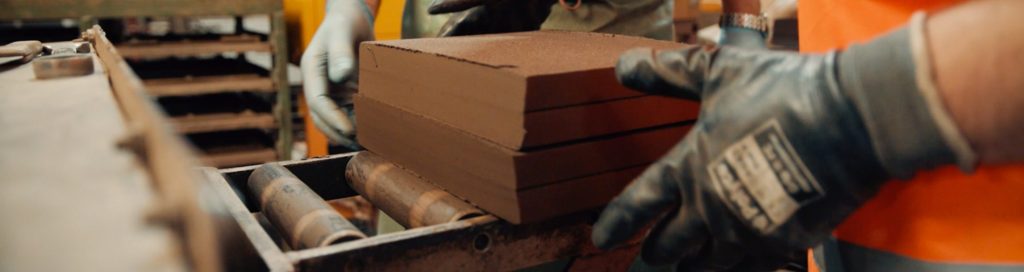
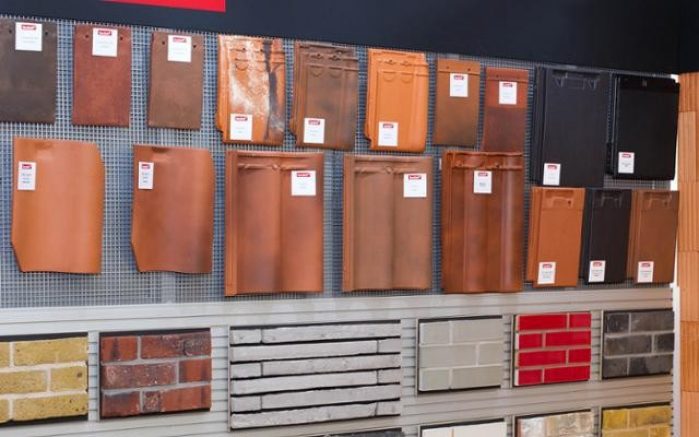
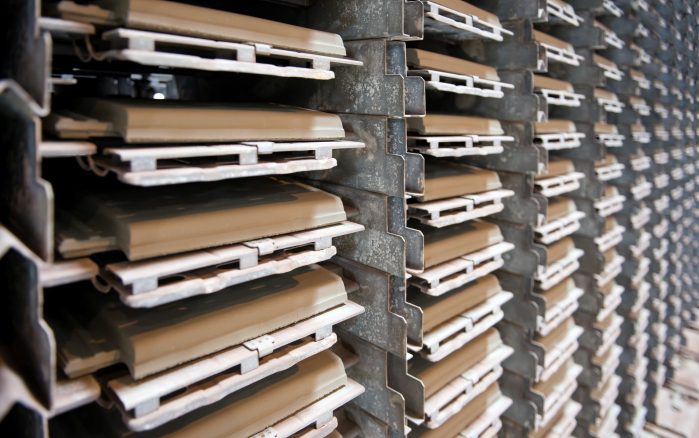