Did you know you can weld lead with anything that’s hot enough to melt lead (327.5C).
Traditionally leadworkers would use a hot iron to join two pieces. These days most leadworkers use a mix of oxygen and acetylene.
There are however various other choices of gasses including hydrogen, propylene or propane available.
Various sizes of bottles holding the gasses are available some as small as one litre and up as far as ten litres.
People often debate weather it’s actually welding or soldering or even braising. A fair explanation of welding vs braising/soldering is: Welding is a fabrication process that lets you join materials like metals by using heat at high temperatures. Welding uses high temperature to join the materials, whereas soldering and brazing do not allow the base metal to melt. After cooling, the base metal and the filler metal get attached.
When welding lead you melt both your base pieces and the filler rod which is also made of lead. The aim at least while I’m personally welding lead is to get full penetration with the heat therefore achieving a strong bond between the joining pieces. There is two options for joining one is called a butt weld where both pieces “butt” together. Alternatively there is the lap weld where one piece overlaps the other. Both are suitable welds providing the bond is strong.
You can weld lead on a workshop bench or in situ, situ welding often calls for vertical welding which is a technique to be mastered with skill. Being able to weld vertical surfaces allows the welder to join pieces far to large for the workshop.
While welding lead toxic fumes are given of and safe precautions must be put in place to protect the tradesman and others around them.
If you are personally interested in learning more about lead welding or lead work in general, Master Roofers is a great place to start.
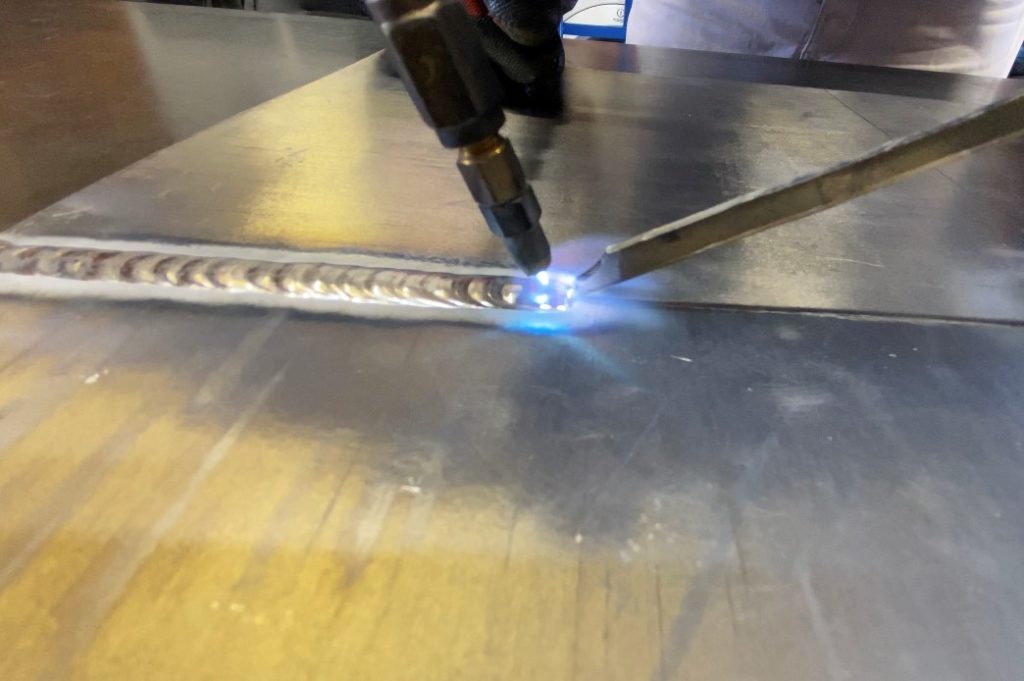
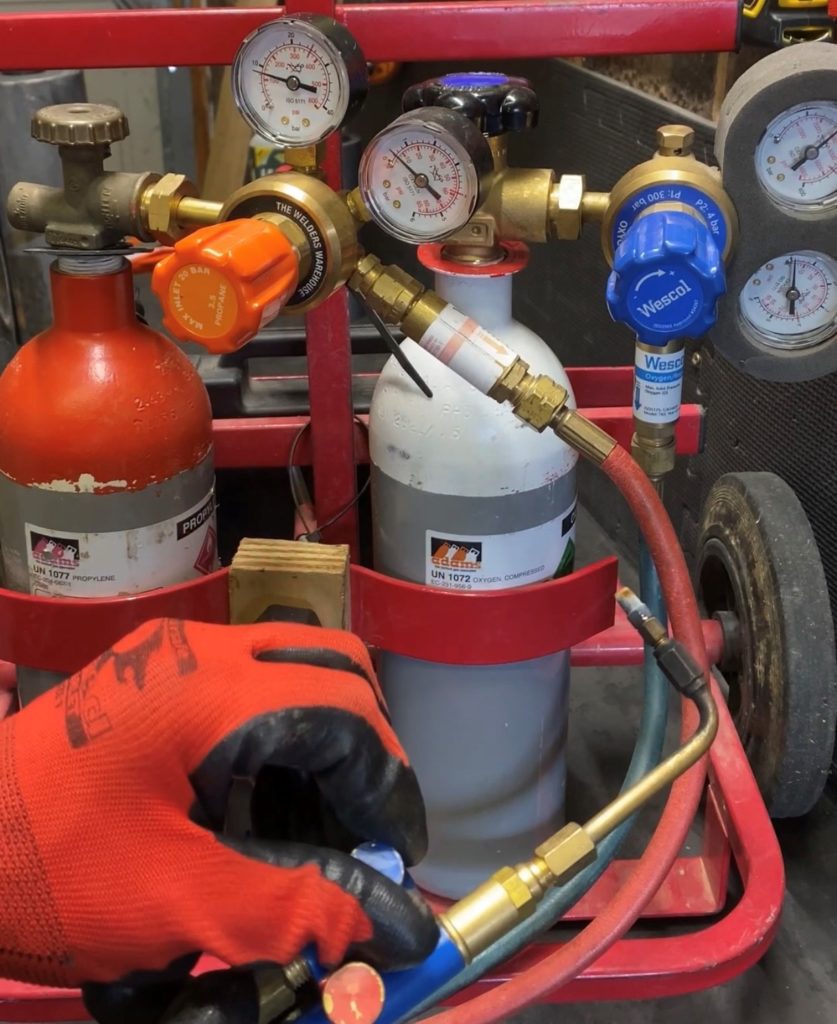
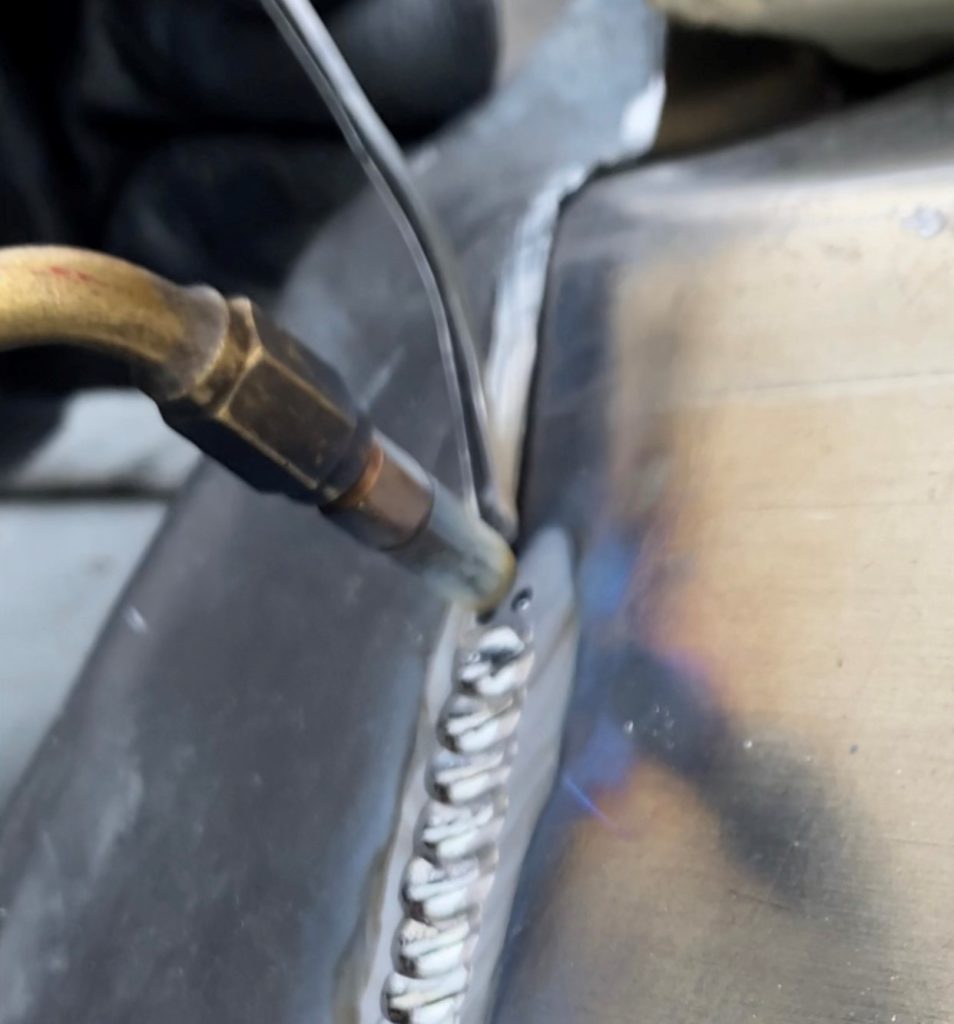