I have written many articles advocating the use of dry fix product such as ridge, hip and verge systems, with all the benefits they bring to modern roof construction. However, we must not forget that mortar has been used in roofing for a very long time. Middle Eastern builders used a material similar to concrete around 1300 BC in coating their buildings with burnt crushed limestone, which set hard as it reacted to gasses in the atmosphere. Cement as we know it today was patented in 1824 by Joseph Aspdin – he called it Portland cement because it resembled Portland stone.
With the right mix of sand aggregate and cement, mortar can produce a very strong bond between building components. But the reason mortar fails in roofing is its inability to cope with differential movement between components; even a well installed mortar-bedded roof junction, using the correct mortar mix, can fail very quickly if any slight movement in the building structure takes place.
Since 2014, BS 5534 has recommended that all mortar-bedded roof components, such as ridge tiles, hip tiles and verges, be mechanically secured to the roof structure using fixings such as nails, screws, or clips. Of course, in many cases, designers, roofers, and clients decide to use a dry fix system and omit mortar altogether. However, there are still many roofs where mortar bedding is desirable for aesthetic and traditional reasons. For example, Edilians has some traditional clay tiles in its range, such as its Phalempin plain tile and classic clay pantile ranges, in many popular colours, that look equally good with mortar as well as with dry fix systems. A great example of combining traditional mortar bedding with mechanical fixing is the Edilians 710 clay angle ridge system; ridge and hip tiles can be installed by mortar edge-bedding combined with a hidden screw and clip fixing into a ridge or hip timber. Equally, Edilians 710 ridges can be used without mortar, with a ridge or hip roll.
What makes a good mortar mix? The strength and durability of mortar is dependent on the type of sand used and even the cleanliness of the water. Sharp sand, also referred to as ‘rough’’, or ‘coarse’ sand, tends to give a stronger mix than soft sand, ie, the type used by bricklayers. The disadvantage of sharp sand is that it is more difficult to work with and to form smooth, neat finishes. Soft sand, often called ‘building sand’, is easier to work with, but it does not achieve the same strength as sharp sand. For these reasons, BS 5534 now recommends a mortar mix using a blend of sharp and soft sands. In a typical three-parts sand to one-part cement mortar mix, the sharp sand should make up at least one-third of the sand content. Alternatively, a building sand can be used that has a distribution of particle sizes similar to blended sand. As a definition, 70% to 90% of the sand should be able to pass through a 0.5mm sieve. There is also the difficulty of defining exactly what sharp and soft sands are, as they vary from region to region. For further guidance, BS EN 13139: 2002; Annex B, categorises sand as coarse, medium, or fine and has tables to define each type.
Hydrated and hydraulic limes are often used in conservation and historical restoration roofing work. Mixed with sand, the lime improves workability and gives a softer, more porous mortar which can be an advantage when working with some softer building materials such as natural stone and terracotta.
Pigments are sometimes added to colour the mortar, though too much will reduce the mortar strength. Generally, colour additives should not exceed one-part pigment to sixty-parts mortar. Proprietary admixtures are also available that improve specific properties of the mortar. For example, plasticizers improve the frost resistance and workability of the mortar. These should be used strictly in accordance with the admixture manufacturer’s recommendations.
Use the correct sand to cement mix and always use clean, potable water. Use admixtures and pigments in accordance with the product manufacturer’s instructions.
In summary, mortar will long have a place in roofing, though it should always be supplemented with mechanical fixings when bedding ridges, hips, and verges. There are exceptions to this rule, for example, some historically or architecturally important old roofs. Also, small scale, or ‘baby’ ridges installed on small roof details, such as porches or bay windows up to a height of 3 metres, can be mortar-bedded without mechanical fixings, provided the self-weight of the ridge tiles is sufficient to resist local wind loads.
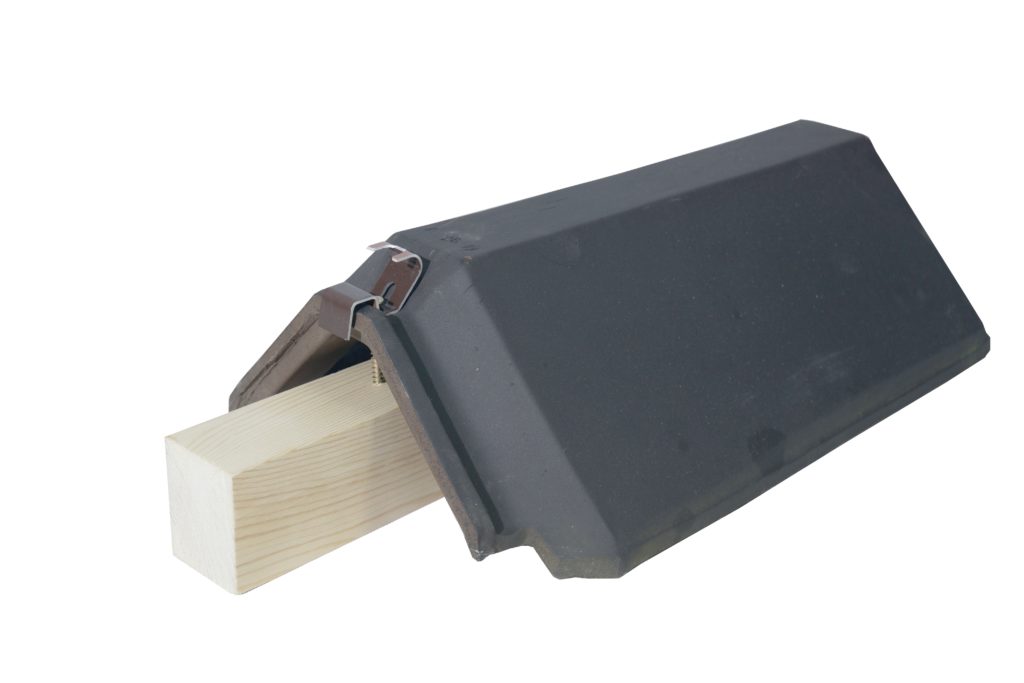
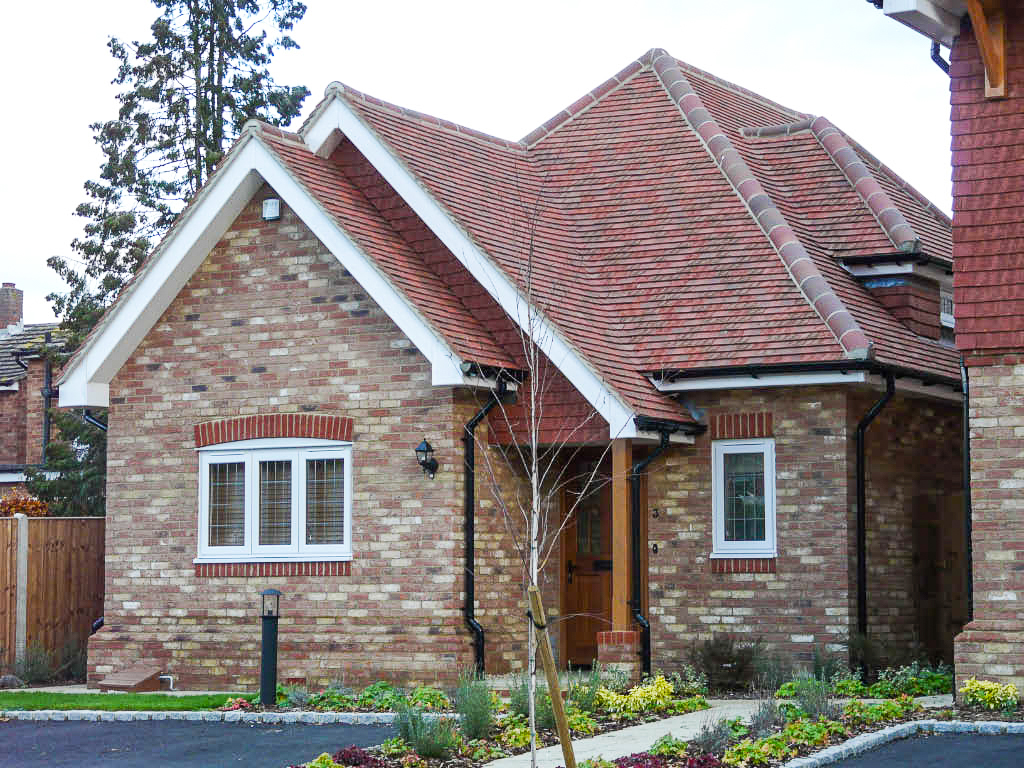