It is estimated that 40% of greenhouse gas emissions in the UK comes from buildings, with 14% of this coming from the housing stock of 28 million homes. Heating and powering buildings currently accounts for 40% of the UK’s total energy consumption.
In June this year, changes to Building Regulations will come into effect which will mean that new homes in England must produce around 30% less net carbon emissions and commercial buildings such as offices and shops around 27% less emissions. Looking even further ahead, in 2025, the introduction of the Future Homes and Buildings Standard will complement the Building Regulations to reduce carbon emissions produced in homes by 75 to 80% less than homes built under current regulations to deliver zero carbon construction. Existing homes will also be subject to higher standards when an extension is added, or thermal upgrades are made.
This all follows a major revision last year to BS 5250: Code of practice for Management of moisture in buildings. In addition to a general update to all parts of the previous Standard, this latest version contains new guidance on moisture risks other than condensation, a whole building approach to moisture-safe design, building context, the coherence of design and detailing interactions, as well as capacity and in-service conditions. It also covers the management of moisture risks in buildings undergoing energy saving measures.
The revision acknowledges key changes in modern building design, such as reduced air permeability of the building fabric and higher thermal insulation, both of which have the potential to increase the risk of condensation. It also considers changes in lifestyle and the greater use of moisture-generating appliances such as showers and internal clothes drying. Climate change is also predicted to add to the moisture risk through milder, more humid winters and more frequent and heavier incidents of driving rain events.
The differences between ‘as designed’, ‘as built’ and ‘in service’ conditions are now more clearly understood and for cold pitched roofs in particular, BS 5250 gives prescriptive guidance based on the evidence of many years of successful use of ventilation products to prevent the harmful effects of excessive condensation build up in the roof structure and loft space.
The gap between design and actual built performance can be attributed to a number of factors, such as overly ambitious assumptions made by the designer, incorrect or careless construction, or poor-quality materials.
A common fault is a lack of ventilation provided into the roof space, sometimes because there is a misconception that the use of a permeable underlay means ventilation is not necessary. There are different types of permeable underlays, all requiring their own methods of installation. The location and level of ventilation required to complement a vapour permeable underlay very much depends on the construction of ceilings. For example, a ceiling with an effective air and vapour control layer, with efficient seals around cable and pipe penetrations, will reduce the potential for excessive water vapour entering the roof space and so a reduced level of ventilation may be required. BS 5250 recommends the use of ventilation in a cold roof structure, ie, where the insulation is laid across a horizontal ceiling, even where a vapour permeable underlay is used.
Another common problem is roof space ventilation being ineffective due to the way it is installed or because the products are poor quality. Rafter rolls, or panel vents, are an important part of any eaves ventilation system in a cold roof. They must be set to ensure that air from the eaves ventilators can pass between the underlay and insulation into the loft space.
The rafter roll must be width enough to accommodate the depth of loft insulation. The effective depth of the insulation at the eaves also varies with the pitch of the roof; for example, the lower the roof pitch, the wider the rafter roll needs to be to accommodate the insulation.
To reduce costs, some rafter roll products end up being of such low quality when thinner materials are used without adequate design and manufacturing methods, leading to products that are poorly formed with insufficient structure that they will collapse when the insulation is installed, reducing or closing off the air path.
At Manthorpe, we have been developing innovative building products for the construction industry for over 30 years. We have extensive experience in the plastics industry, with the expertise to design and manufacture virtually all our building products in-house and continue to invest heavily in new technology and cutting-edge machinery and production processes. This enables our team to be at the forefront of product development, driving industry progress through precision and innovation.
The Manthorpe G500 series of Roll Panel Vents is an excellent example of our commitment to design and quality. The range is designed to maintain the necessary air gap between the underside of the roofing membrane or sarking board and loft insulation at the eaves to ensure a continuous flow or air into the roof space. The castellated profile of the Manthorpe Roll Panel Vents is suitable for 400mm, 450mm, or 600mm rafter centres and strengthening ribs ensure it is strong enough to maintain its profile shape. Each panel rolls out in one continuous 6 metre length and is ideal for both new build and refurbishment where the rafter centres are inconsistent or unknown.
The G500 range is available in several widths, 325mm, 650mm, 800mm through to the G504 which is 1250mm wide, making it ideal for low pitched roofs and deeper insulation. Of course, panel vents can be combined to provide any required width.
For further information please visit our website at www.manthorpebp.co.uk or contact our sales and technical support advisors on 01773 303 000 or email us at mbp.care@manthorpebp.co.uk.
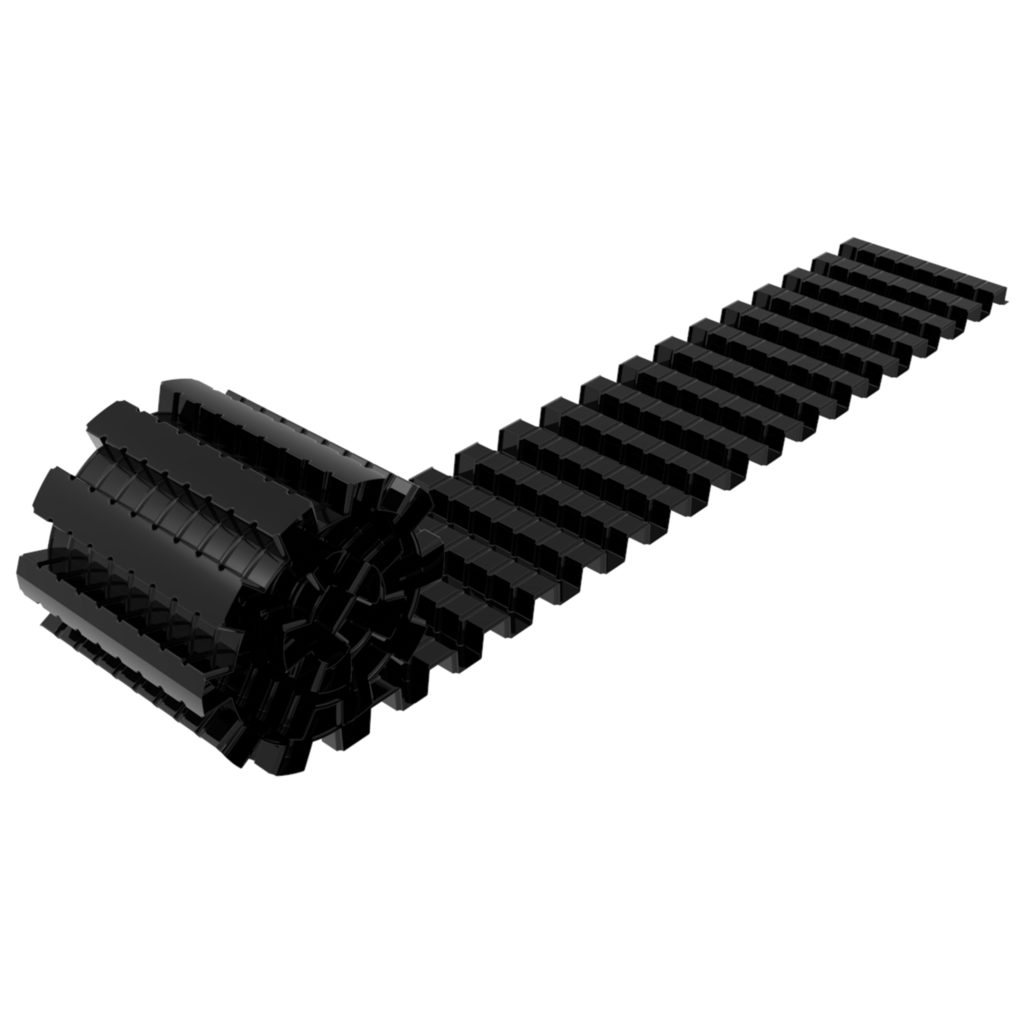
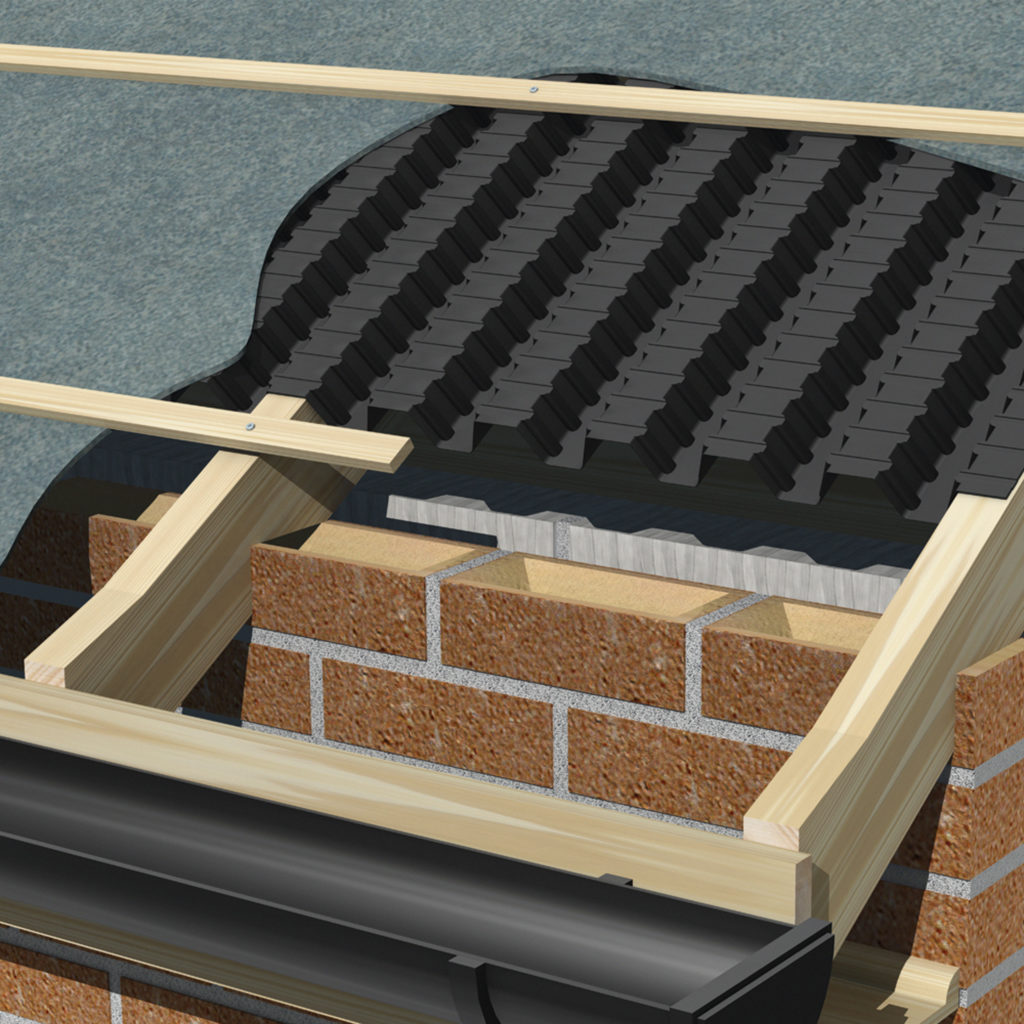
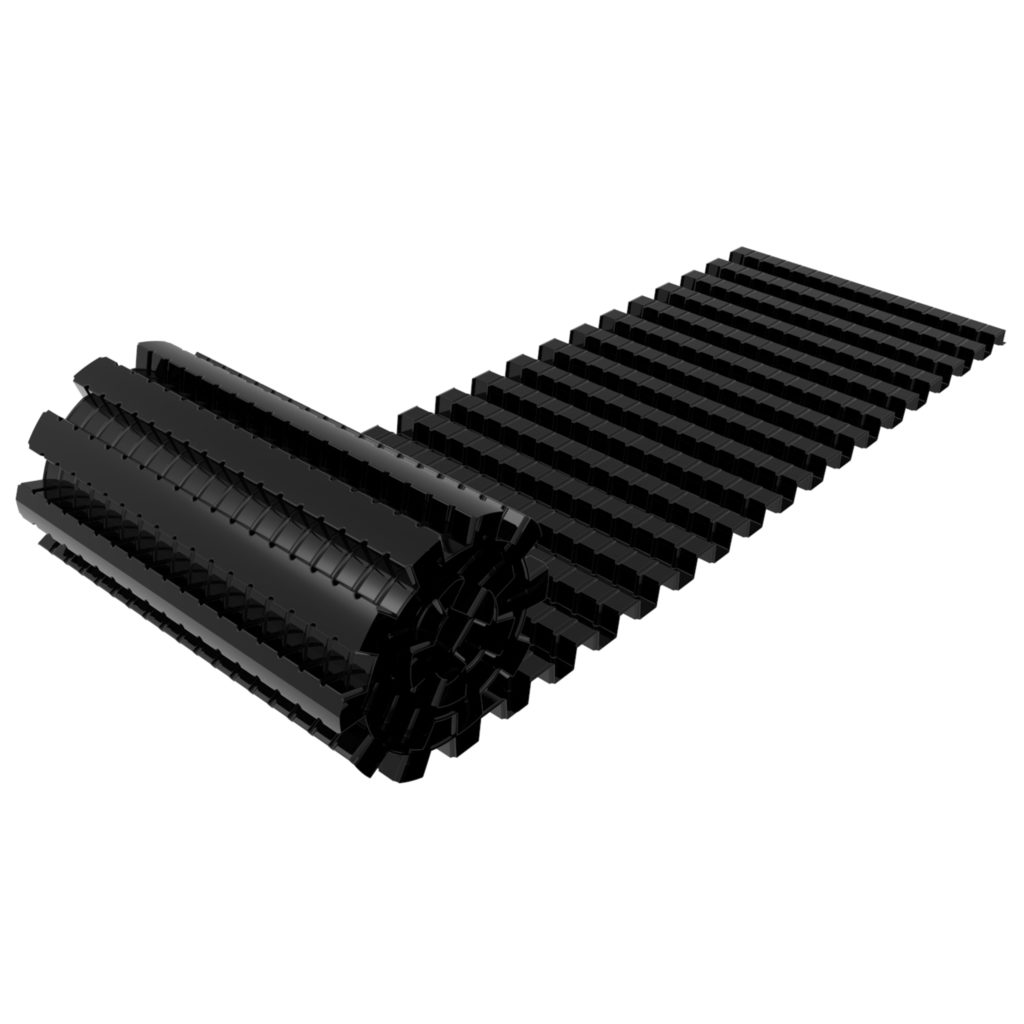
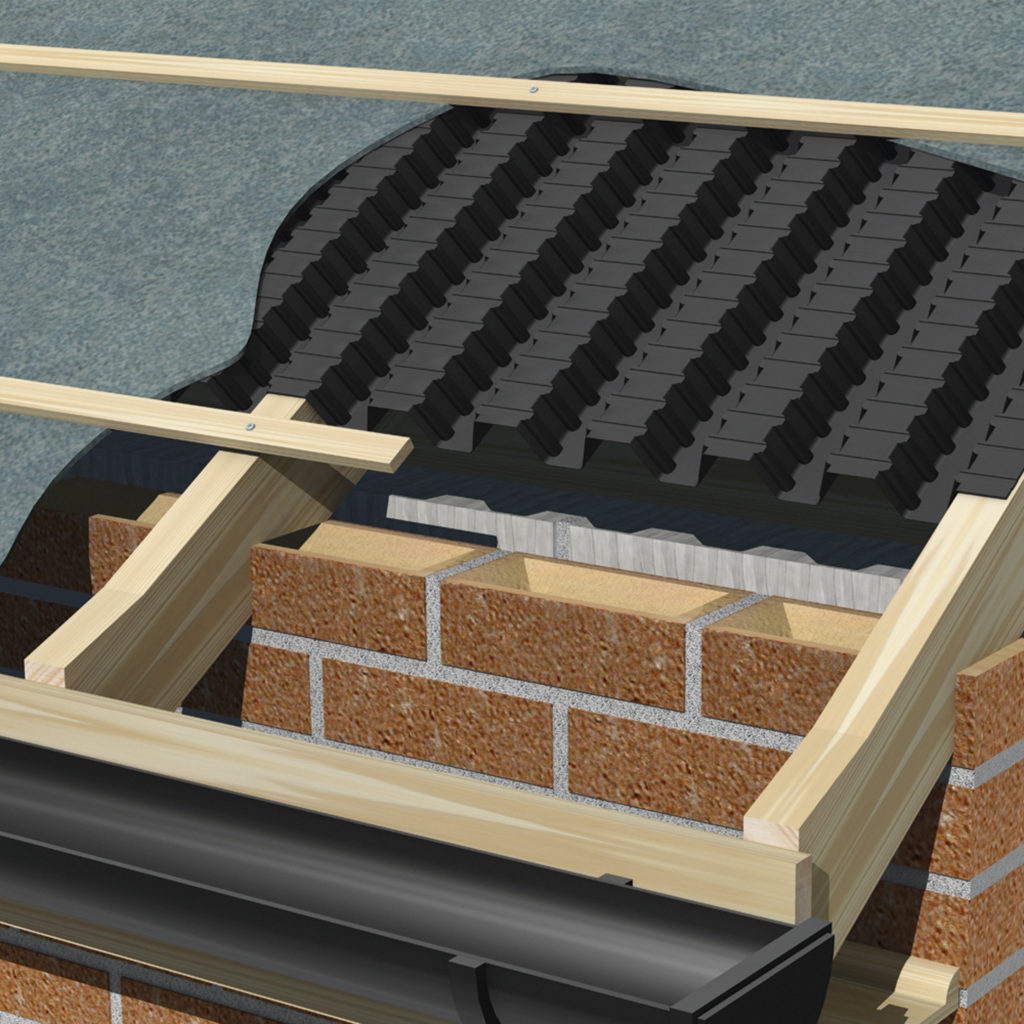
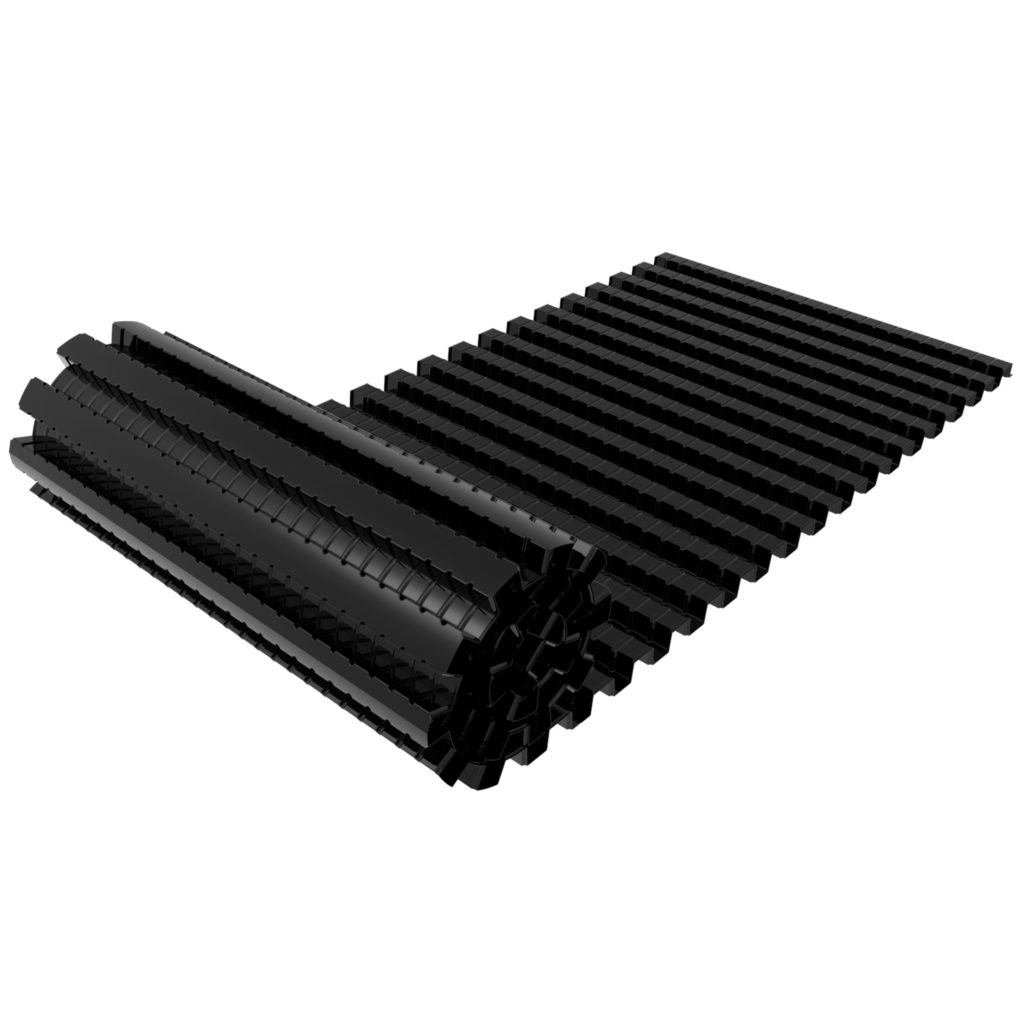
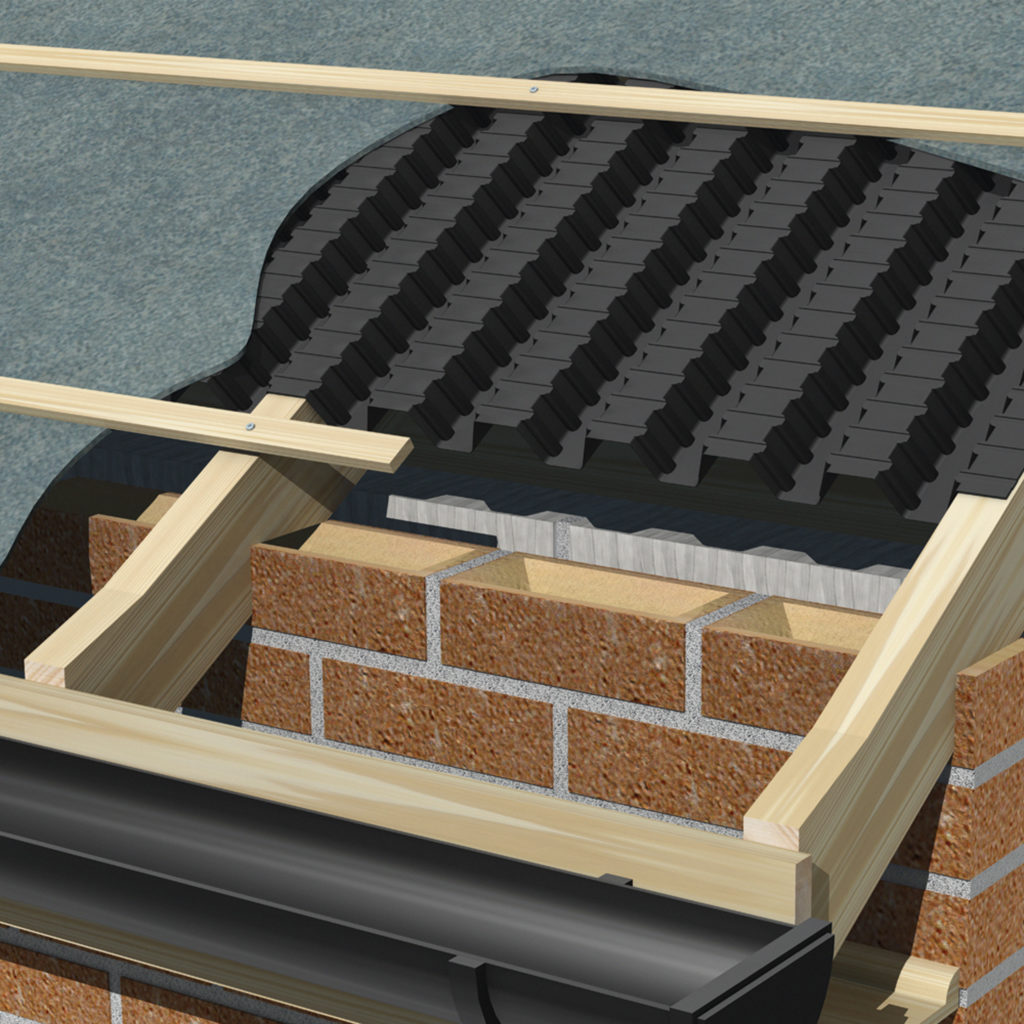
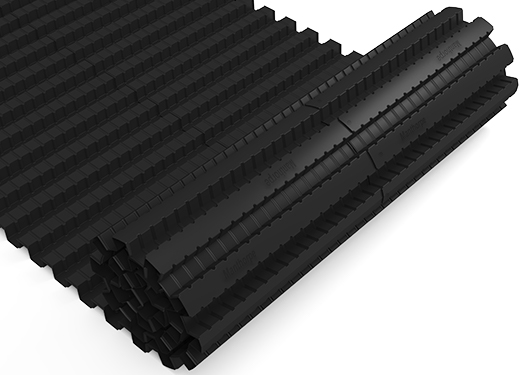
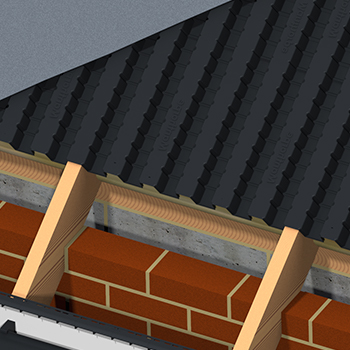